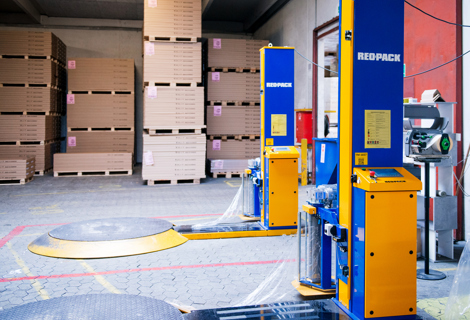
Upgrade of End-of-Line Production
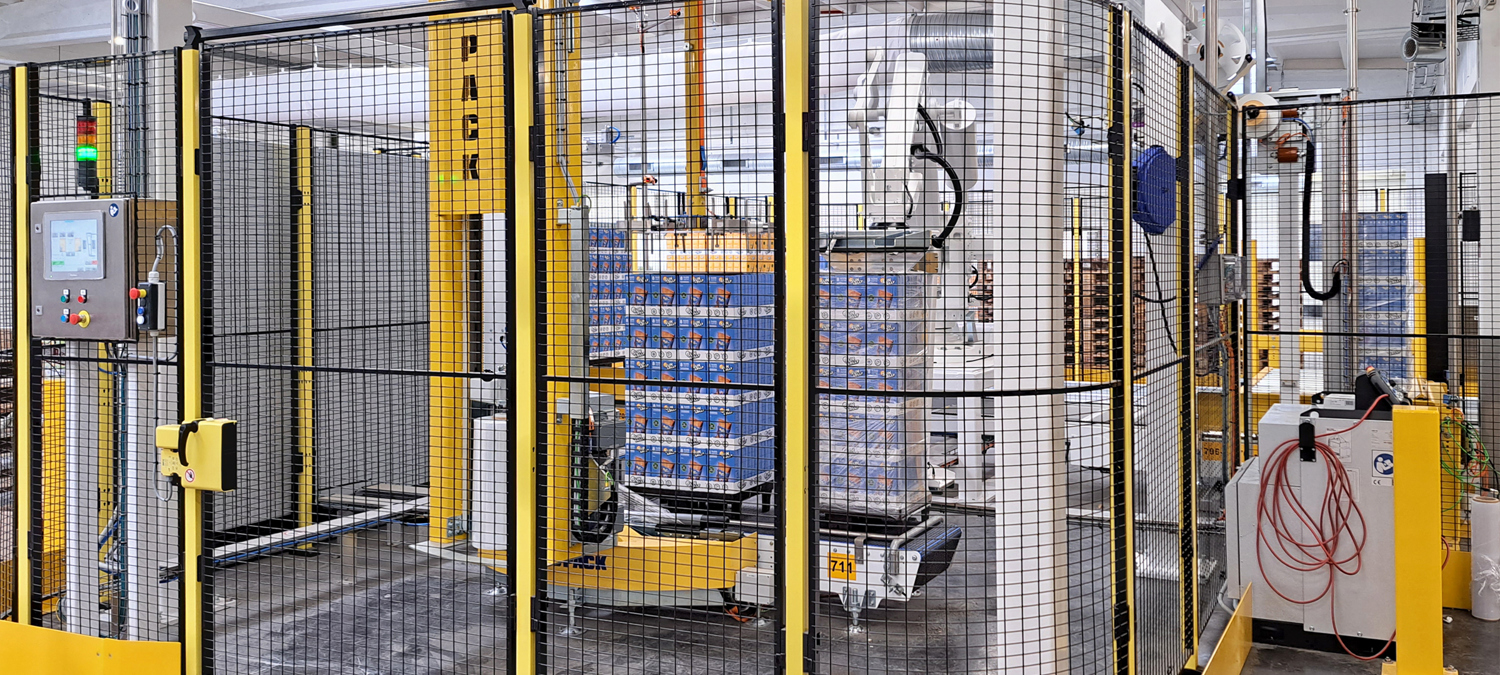
CO-RO optimised End of Ice Packaging line
At CO-RO in Frederikssund, they have upgraded their "End of Ice Packaging line" by fully automating a significant part of the processes in their Lolly department. This has resulted in increased productivity and capacity, created uniformity in products, and improved the working environment for their operators.
Increased productivity
Improved working environment
Higher quality and uniform products
Challenge
The end-of-line process was carried out with machines over 20 years old – and in a resource-intensive facility that involved many manual functions, especially regarding pallet handling.
Solution
The facility includes a stretch wrapper with top film applicator, a new label printer for fully automatic pallet labeling at variable heights, and additional buffer conveyors for pallets.
Benefit
The upgrade has resulted in increased productivity and capacity, created uniformity in products, and improved the working environment for their operators.
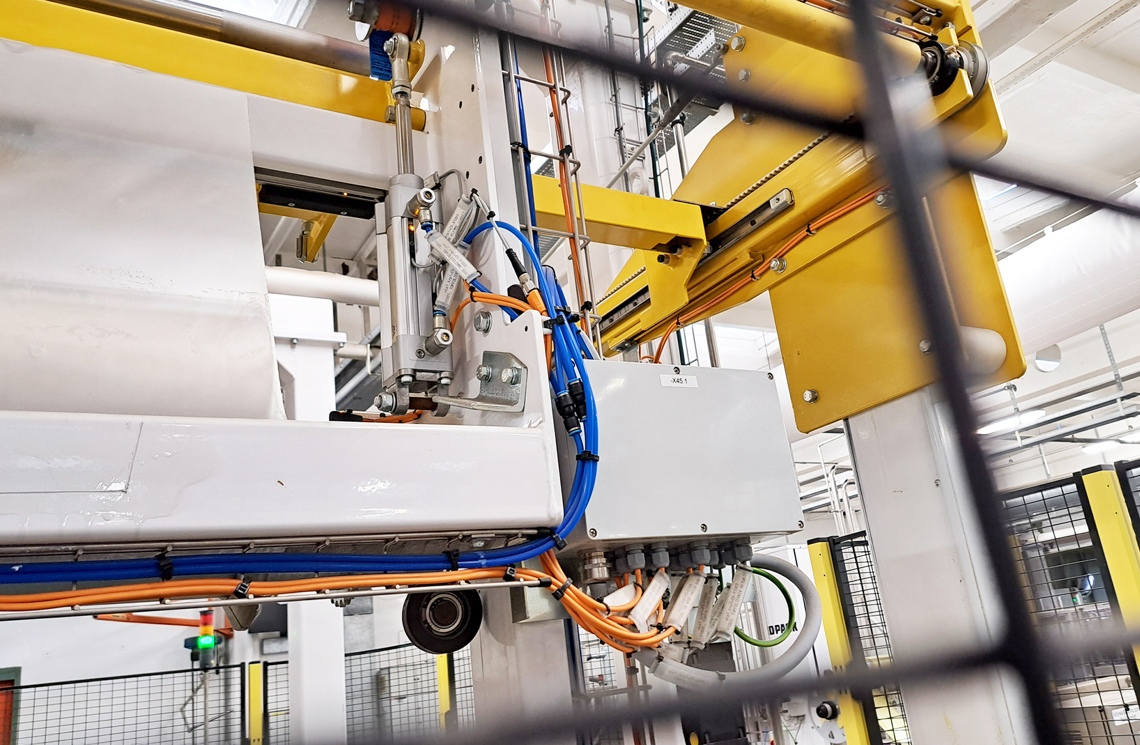
From manual to automatic set-up
CO-RO is a major producer of fruit-based beverages and do-it-yourself ice cream, delivering approximately 180 million units globally each year. Due to the growing demand for Sun Lolly ice cream, there is a need to produce even more ice cream than before. This is one of the reasons why CO-RO has upgraded their existing "End of Ice Packaging line" by fully automating the system with a solution provided by REO-PACK.
Before upgrading to the new system, the process involved machines over 20 years old and a resource-intensive facility with many manual functions, especially regarding pallet handling.
This manifested in numerous labour-intensive processes, both in terms of manually setting up the robot for the current production by selecting pallet type, box type, and the number of layers on the pallet, and when the robot needed to be fed with pallets and the removal of pallets. CO-RO also faced a challenge with insufficient buffer capacity on the pallet conveyors, resulting in time-consuming back-and-forth movement of pallets. Empty and finished pallets also had to be transported to and from the robot, then to and from the stretch wrapper, application of top film, securing the film to the pallet, and replenishing with empty pallets. Additionally, pallet labels had to be manually retrieved from production papers and printed before being manually applied to the pallets.
The many manual tasks naturally impacted the working environment, which was one of the reasons for this upgrade. With a desire to increase capacity, eliminate heavy lifting and monotonous repetitive work, as well as improve poor working postures in general, a decision was made to invest in a fully automated system. REO-PACK was chosen for the project as they could manage all aspects of the project. However, the robot in this solution was supplied by another vendor, as CO-RO wanted to use their previously familiar robot supplier.
In the packaging department of the Lolly section, a fully automated system has been installed with pallet magazines for each of the three pallet types, a ¼-pallet crane capable of placing 4 ¼-pallets on top of a Euro pallet, a couple of transfer carts, and buffer conveyors for waiting pallets. Additionally, the system includes a stretch wrapper with an integrated top film applicator, a new label printer for fully automatic pallet labeling at variable heights, and finally, more buffer conveyors for finished pallets. The automation throughout the system has been upgraded so that all system components, via D365 and MES, are now set up fully automatically for production through the current job on the line. This job contains all data about pallet type, box type, wrapping patterns, and all other processes in the packaging department.
CO-RO increases productivity and enhances working environment
The fully automated system has contributed to increasing both productivity and capacity while improving the working environment for operators by eliminating the majority of heavy lifting and manual processes. The automation has simultaneously enhanced product quality and created uniformity in the products.
The new system also opens the doors for expansion with additional production lines as needed, as the system has significant overcapacity compared to the current ice cream production. An expansion of the facility is already in the planning and construction phase.

Explore what we have done for other companies
With dedicated employees, we ensure efficient service at the highest level, no matter where you are in the world.
Call us at +45 9858 4100
Contact us
We are ready to answer your questions
and have a non-committal conversation
about the possibilities of incorporating
a stretch wrapper in your company.